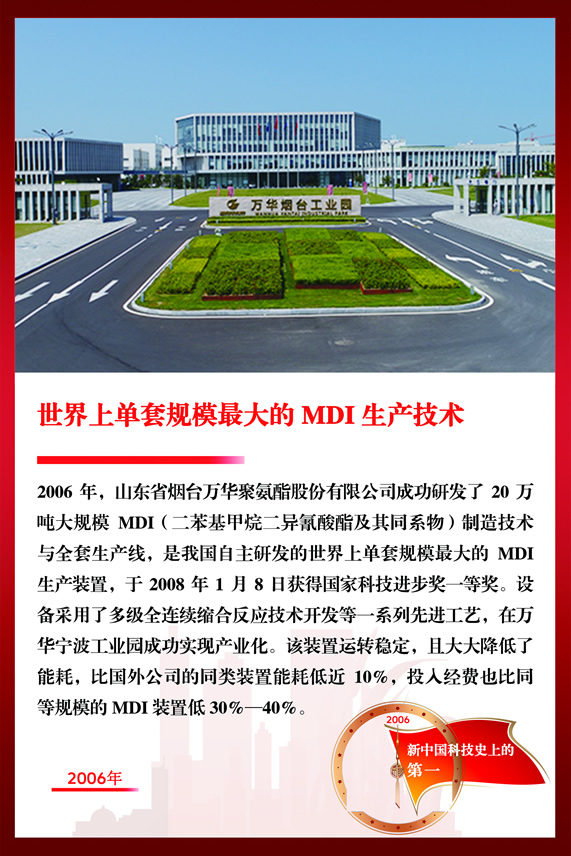
成果简介 2006年,山东省烟台万华聚氨酯股份有限公司研制开发了20万吨大规模MDI制造技术与全套生产线,并于2008年1月8日获得2007年国家科技进步奖一等奖。这套生产线是目前国内依靠自主创新、自力更生制造的产量最大的MDI生产装置,打破了国外技术垄断,使我国成为继美、德、日之后第四个掌握MDI制造技术的国家。设备采用了多级全连续缩合反应技术开发等一系列先进的工艺和技术,在万华宁波工业园成功实现产业化,装置运转稳定,且大大降低了能耗,比同类跨国公司的能耗降低了近10%,同等规模的MDI投资也比跨国公司低30%—40%。20万吨/年的MDI成套生产技术已成为世界上单套规模最大的MDI生产技术,也是世界上最先进、最成熟的MDI技术,标志着我国的MDI生产技术已跨入世界MDI制造技术的领先行列。 历史背景 自MDI是二苯基甲烷二异氰酸酯及其同系物的英文缩写,以其为原料制备的聚氨酯由于具有优异的性能被广泛应用于国民经济各个领域。20世纪以来,随着我国建筑、汽车、制冷、合成革、制鞋、胶粘剂、涂料及纤维等行业的快速发展,市场对MDI的需求也迅猛增长。而作为高技术、高资本、高附加值的MDI产品,其核心生产技术复杂,长期被几大跨国公司垄断。
20世纪70年代末,烟台万华从日本引进一套相当于60年代国际技术水平的年产1万吨MDI生产装置。由于不能掌握核心技术,装置运行十分艰难,十年未能达产。从20世纪80年代开始,原国家计委先后批复4套引进技术建设MDI项目,都因跨国公司技术封锁而相继失败。1993年,烟台万华发现十年前引进的装置寿命已到期,而新技术引进无门,技术创新没有大的突破,产品明显缺乏市场竞争力,要想改变,就只能走自主创新的研发道路。 创新历程 同1993年9月,万华开始攻关MDI装置的核心技术,不断从落后的年产1万吨MDI生产装置中汲取有用经验,通过消化吸收再创新,连续取得了一系列技术突破。1994年产能近9千吨,1995年达到1万吨。当1996年产能达到1.5万吨时,标志着万华已经完全消化了之前日本引进装置的技术。1998年底,国家有关部门同意公司实施股份制改造,新机制为技术创新提供了良好的环境和动力,创新步伐明显加快。
2001年10月,科技部将年产16万吨MDI制造技术开发项目列为国家科技攻关计划引导项目。2002年烟台万华的MDI装置产能突破8万吨,但与国外同行业公司相比,技术水平仍有一些差距。在国家发改委18亿元贴息贷款及各级政府的支持下,公司决定在宁波大榭岛兴建16万吨MDI装置,并在技术和工艺方面赶上或超过国际先进水平。在国家、山东省和烟台市科技部门的支持下,烟台万华聚氮醋股份公司科研人员努力攻关,于2006年开发出了16吨/年的MDI制造技术,同年开发出了20吨/年的MDI制造技术,并将成果成功应用于工业化生产,申请专利24项,其中发明专利17项,建成了我国第一套具有国际规模的MDI生产装置,使我国成为少数几个拥有大规模制造技术自主知识产权的国家之一。
我国MDI装置生产工艺在三个方面成为世界首创:一是完全摒弃了引进时的间歇工艺,缩合、光气化和结晶分离装置实现了全连续;二是通过实施能量集成和工艺优化,使装置公用工程消耗达到并部分超过了国外公司的技术水平,原料消耗与国外处于同一水平;三是取消了液态光气储罐,使系统内静态光气储量为零,极大地降低了装置的安全风险。同时,该装置在连续缩合、高效液膜射流光气化、精馏结晶一体化三项关键技术上达到国际领先,在采用废CO2制备CO技术上达到国际先进,并在全球首次实现废盐水循环利用。 重大意义和深远影响 年产20万吨大规模MDI生产技术开发及产业化生产,打破了国外对我国MDI技术长达40年的封锁,使我国在该领域拥有了自主知识产权和民族品牌,成为继美国、德国、日本之后第四个拥有大规模MDI技术的国家,不仅推动了全球MDI产业的技术进步,还扭转了我国MDI长期依赖进口的局面,拉动了下游产业,带动了中国聚氨酯工业及相关行业的发展。MDI技术的突破,标志着我国大型石化装置可以不再全部依赖进口,中国完全有能力自主研发建设,对我国化工工业自主创新具有典型的示范意义。
|