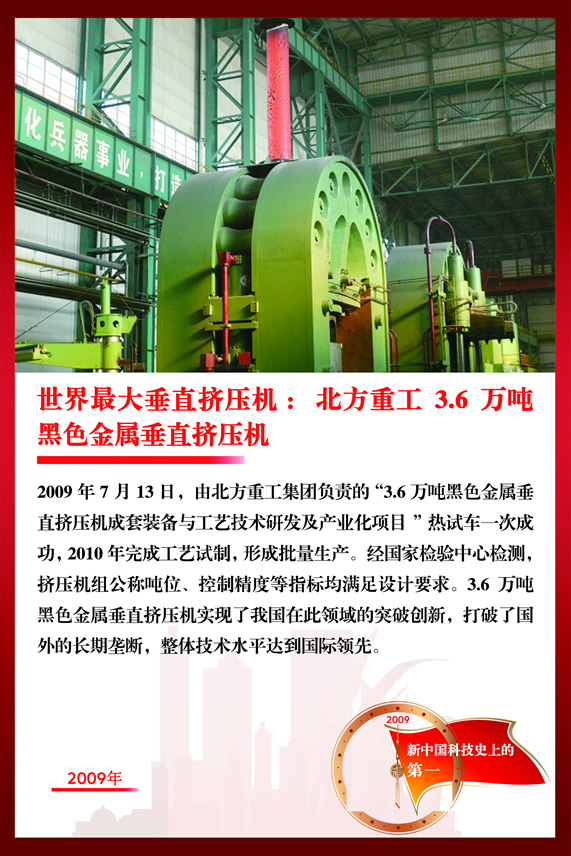
成果简介 3.6万吨黑色金属垂直挤压机成套装备与工艺技术研发及产业化项目于2009年7月13日热试车一次成功,2010年完成工艺试制,形成批量生产。经国家检验中心检测,挤压机组公称吨位、控制精度等指标均满足设计要求,其部级鉴定和行业评价为“开创性地运用预应力钢丝缠绕和剖分—坎合技术,成功研制了世界上最大的3.6万吨黑色金属垂直挤压机,实现了我国在此领域的突破创新,打破了国外的长期垄断,整体技术水平达到国际领先”。 历史背景 2003年,中国工程院《发展我国大型锻压装备研究》报告指出:“大型难变形金属挤压机在我国还是一个空白,已经制约了相关武器装备尤其是军用先进航空发动机的发展”。同期相关报告显示,当时我国60万千瓦以上超临界、超超临界火力发电设备必不可少的耐高温高压大口径厚壁特种钢管90%以上依赖进口。“十一五”期间乃至相当长一段时间,我国发电设备制造每年需此类钢管约10多万吨。因此,建设一条重型挤压生产线,对实现国家急需关键材料的国产化意义重大,可为电力、石化、航空航天、军工等行业自主发展奠定高端材料基础。重型挤压技术是高性能、难加工材料的核心加工技术,工艺复杂、设备建造难度巨大。当时,美国威曼高登公司对其形成长期独家垄断,并称其为公司的核心技术,不对外转让。而自称拥有设计能力的德国公司则漫天要价,令人生畏。在此背景下,厚壁无缝钢管的国产化重任落到了北重集团身上。作为共和国最大的火炮研制和生产基地,全国的火炮炮身大型锻件都出自北重集团。多年来,北重集团在特种钢制造领域积累了丰厚的技术储备,并利用炮钢技术开发了大口径厚壁无缝钢管。但该技术效率比较低,同时还面临着大规格管材很难被加工的困扰。面对巨大的市场需求和外国同行的封锁,北重集团没有退缩,主动请缨,提出自主研制3.6万吨黑色金属垂直挤压机这一大国重器。 创新历程 重型挤压生产线包括一台3.6万吨垂直挤压机及63台套相关辅助设备。作为世界的首台首套工程,可借鉴的现成经验极少,不管是在施工建设、设备制造、安装运输方面,还是在设备调试、人员培训、工艺工装方面,来自方方面面的压力无时不在。作为国家重大科技专项“3.6万吨黑色金属垂直挤压机装备及工艺技术研发”的课题组长,雷丙旺秉承着“不能让外国人小看我们”的信念,带领清华大学等国内20余家单位组成的课题组,向极端制造发起挑战,成功攻克大口径厚壁无缝钢管挤压工艺和重型挤压装备的设计、制造两大技术难题。仅用3年时间,就完成了国外设计制造同类设备7年的工作量。在这三年时间里,研发团队没有周末、没有节假日,从白天到黑夜,从深夜到黎明,团结协作,集智攻坚,不断克服技术、设备、安装调试等多个重大难题,挤压机终于在2009年7月13日热调试成功。
在成功打造3.6万吨黑色金属垂直挤压机这一“大国重器”的基础上,雷丙旺凭借自己丰富的冶金技术经验,带领技术团队,对航空发动机涡轮盘关键材料挤压技术进行了艰苦攻关,克服了试制中出现的各种问题,实现了这一技术的跨越式发展并达到世界先进水平。目前该技术已应用于国内大量亚临界、超临界和超超临界火电机组的四大管道,实现了国家超(超)临界火电站四大管道所需管材全部国产化的目标,彻底扭转了国家超(超)临界火电站建设所需P92管材长期依赖进口的局面,且市场价格由每吨十几万元(人民币)降至每吨几万元,每年为国家节约资金40亿元,创造了巨大的经济效益。 重大意义和深远影响 首台首套3.6万吨黑色金属垂直挤压机大大提升了我国在世界锻压界的学术地位,彻底解决了高端电力管道自主供应这一重大问题,取得了巨大的经济社会效益,为我国电力行业的健康发展做出重大贡献。该项目该技术入围“中国制造2025”强基工程,是国家能源局确定的国产化示范产品,获国家科学技术进步奖二等奖、省部级一等奖及中国工业大奖表彰奖
|