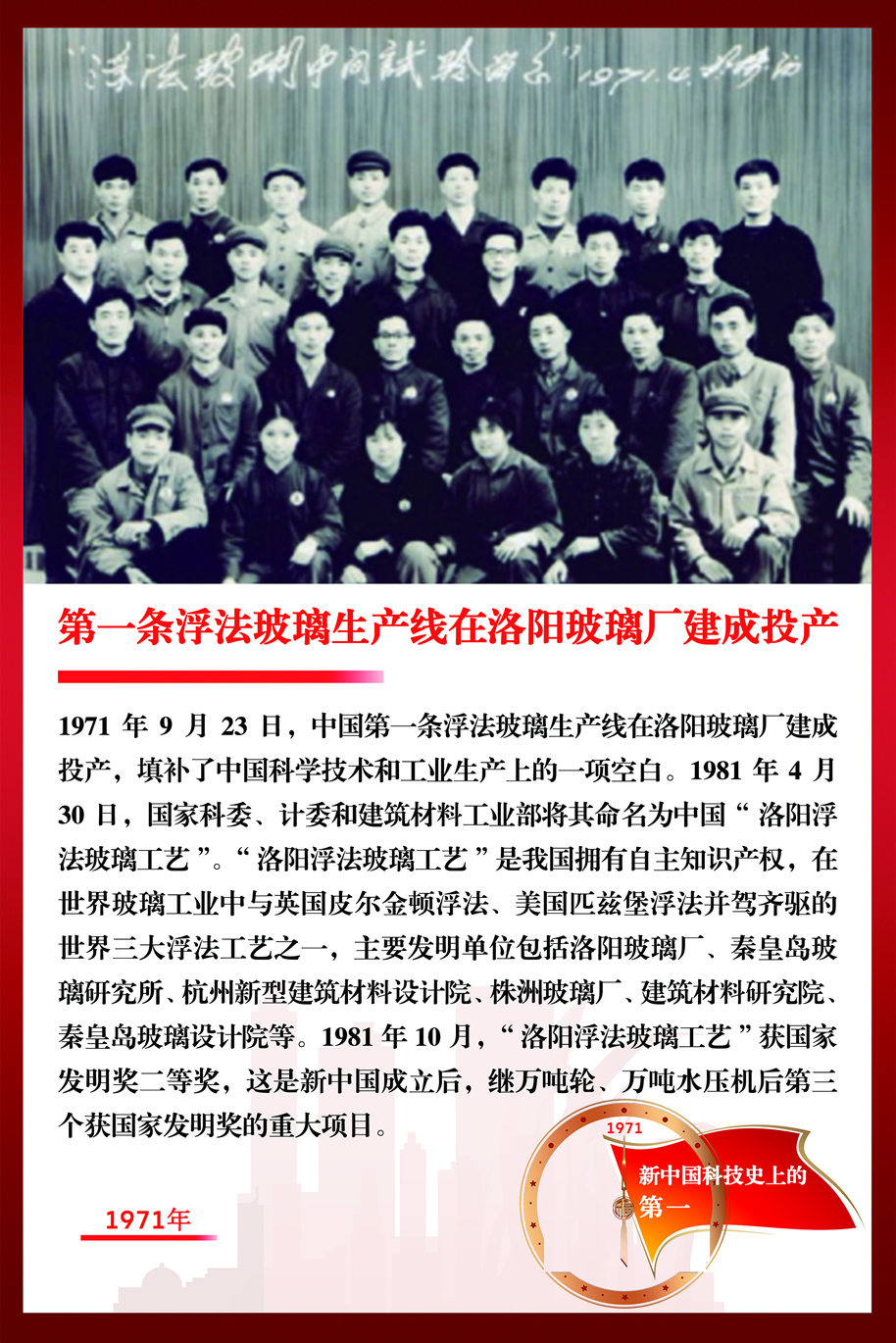
成果简介 1971年9月23日,中国第一条浮法玻璃生产线在洛阳玻璃厂(简称 “洛玻”)建成投产,填补了中国科学技术和工业生产上的一项空白,在我国平板玻璃发展史上写下了光辉的一页。1981年4月30日,国家科委、计委和建筑材料工业部(简称“建材部”)召开技术鉴定会,将这种工艺命名为中国“洛阳浮法玻璃工艺”。同年10月,“洛阳浮法玻璃工艺”获国家发明奖二等奖,这是新中国成立后,继万吨轮、万吨水压机后第三个获国家发明奖的重大项目,获奖单位包括:洛阳玻璃厂、秦皇岛玻璃研究所、杭州新型建筑材料设计院、株洲玻璃厂、建筑材料研究院、秦皇岛玻璃设计院。 历史背景 20世纪50年代,英国皮尔金顿兄弟有限公司创造了浮法玻璃生产工艺。其工艺具有产品质量高、生产效率高、产品规格多等优点,被誉为平板玻璃工业的一次革命。当时,我国平板玻璃工业十分落后,虽然恢复、扩建、新建了几个平板玻璃厂,但年产量只有几百万重量箱,远不能满足国民经济发展的需要。1964年我国以商务代表名义派员赴英国、德国、法国和荷兰等西方国家考察,向皮尔金顿公司提出购买“浮法玻璃技术”专利事宜未果。我国民族玻璃工业发展受到列强重重技术封锁,只能依靠自己。至此,自主研发“浮法玻璃技术”提上议事日程。 创新历程 1960年,原建筑材料工业部建筑材料科学研究院(以下简称“建材院”)开始收集研究有关浮法玻璃工艺的信息。1965年,建筑材料工业部玻璃工业设计院(以下简称“玻璃院”)玻璃工艺二室派选工艺、窑炉、机电、煤气等专业技术人员参加建材院玻璃室的浮法玻璃试验工作,正式开展浮法玻璃实验室阶段研究。项目组在一无可借鉴资料、二无国外相关技术情报、三无现成浮法玻璃样品的情况下,克服重重困难,先后攻克了“高温玻璃液通过锡槽时容易凝结,造成玻璃厚薄不均”“玻璃无法拉宽拉平”等关键性技术难题,改进了几十个技术方案,进行了成百上千次的试验,逐渐掌握了“玻璃液-锡液-保护气体”气液固三相系统在高温环境中的表面物理化学行为,试验取得重大进展。
“文化大革命”开始后,科研环境受到严重破坏。科研人员排除干扰,迎难而上,开始了2t/d玻璃电熔窑的建造和8m锡槽的建造和浮法研究实验工作。通过一系列半连续工艺试验和连续性工艺试验,解决了浮抛介质、保护气体的成分和净化、玻璃成分、加热元件、锡槽结构和耐火材料的选取等技术难题,1967年终于获得了一系列试验室阶段性成果,最终拉出了200—250mm宽的浮法玻璃带,并为下一步工业化中间试验奠定了理论及技术基础。 半工业性中间试验于1968年2月正式开始在株洲玻璃厂进行,由株洲玻璃厂、建材院和玻璃院3家单位的人员组成试验班子,着手改建球窑和各项试验的准备工作,由建材院负责试验用锡槽的设计,其余包括玻璃熔窑改造、成型用的压延机、退火窑和相应的土建、水暖电以及保护气体等全部配套设计工作均由玻璃院承担。经过2年的努力,试验取得了突破性进展,其中最主要的成果是形成了浮法玻璃的成形方法——玻璃液直接流入法,并拉引出中国第一批6mm浮法玻璃样品。同时,在流槽的安装、槽体的构造、雾点的消除以及操作方法和工艺制度等多方面都取得了相当丰富的经验和成果。
在中试基础上,研发团队在洛玻进行了工业化试生产。1971年9月,80t/d浮法玻璃生产线胜利投产,成功拉引出原板宽近2m、厚6mm的质量较好的浮法玻璃,投入市场后取得良好的经济效益。1971—1980年,经过设计院、研究院和工厂等多家单位的共同努力,洛阳一线经过两次冷修改造,玻璃熔窑实际熔化量由90t/d提高到250t/d,玻璃原板从最宽1300mm达到2400mm,可生产玻璃厚度增加到3—6mm,实现了产品质量稳定的商业化生产。技术上完善了锡槽的成形方法,取得玻璃展宽、拉薄和稳定产品商业化生产的成果;在退火、冷端切裁、全线的机械化和自动控制方面开发了一些浮法专用的机电装备和材料;保护气体由净化煤气发展为氮加氢(N2+H2),系统掌握了浮法玻璃相关工艺和关键装备制造技术,洛阳浮法工业性试验生产线取得了丰硕成果。 重大意义和深远影响 “洛阳浮法玻璃工艺”是我国拥有自主知识产权,在世界玻璃工业中与英国皮尔金顿浮法、美国匹兹堡浮法并驾齐驱的世界三大浮法工艺之一。主要发明单位(建材科学研究院、秦皇岛玻璃研究所、杭州新材院、秦皇岛玻璃设计院和株洲玻璃厂、洛阳玻璃厂)经历了艰难的探索,用智慧和汗水让“洛阳浮法玻璃工艺”在中华大地上诞生。经过50年的风雨砥砺,该技术不断得到发扬光大,通过自主创新先后研发了超厚和超薄浮法玻璃技术、大规模浮法玻璃技术、在线镀膜改性技术、浮法特种玻璃等,成功为我国玻璃工业的发展壮大竖起了一座雄伟的丰碑。
|