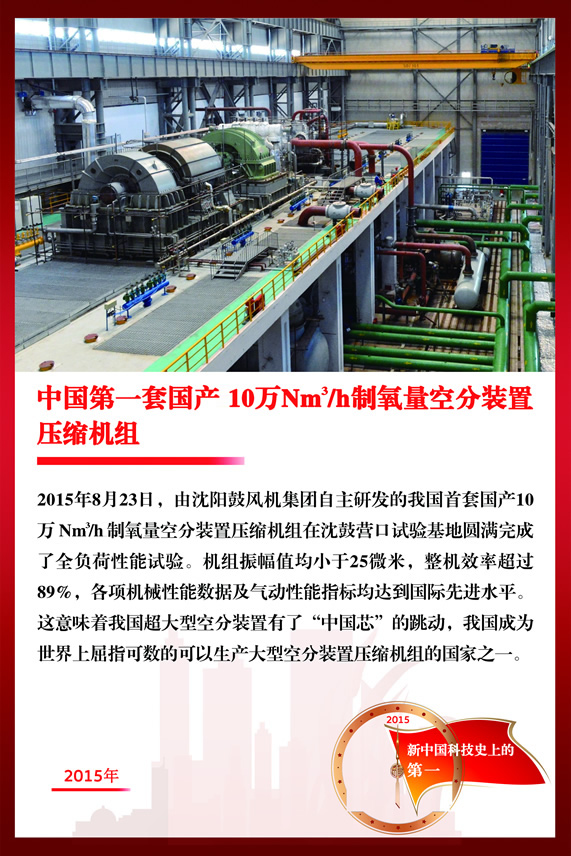
成果简介 2015年8月23日,由沈阳鼓风机集团自主研发的我国首套国产10万Nm3/h制氧量空分装置压缩机组在沈鼓营口试验基地圆满完成了全负荷性能试验。机组振幅值均小于25微米,整机效率超过89%,各项机械性能数据及气动性能指标均达到国际先进水平。这意味着我国超大型空分装置有了“中国芯”的跳动,我国成为世界上屈指可数的可以生产大型空分装置压缩机组的国家之一。 历史背景 我国是一个“缺油、少气、富煤”的国家,发展煤炭深加工可以使我国减少对进口石油和天然气的依赖,是调整我国能源结构的重要路径。将煤进行气化处理是煤炭深加工的首要步骤,需要耗费大量的氧气。氧气通过空气分离获得,而压缩机则是空分装置的“心脏”设备。国家在建设煤化工项目中,需要大量10万Nm3/h等级的空分压缩机组,然而,其核心技术长期被少数外国公司垄断,我国大型空分装置压缩机组全部依赖进口。
2011年10月底,针对神华宁煤400万吨/年煤炭间接液化项目,国家能源局组织了关键设备国产化的工作会议。会议决定将10万Nm3/h空分装置及其配套的压缩机机组的国产化任务托付给沈鼓集团。此次10万Nm3/h空分压缩机国产化的成功与否关系到我国煤炭深加工的发展,因此,沈鼓集团集中优势资源,迅速成立了一支由优秀专业技术人员组成的强大研发团队,具备多年重大项目实战经验的沈鼓集团设计院总工程师、辽宁青年科技奖十大英才获得者汪创华,担任了本项目的总设计师。 创新历程 沈鼓集团多年的技术积累为本次项目研发奠定了稳固的基础。2004年,在无合同的条件下,沈鼓集团自筹资金完成了3.5万空分齿轮组装式原料空气压缩机样机的开发、制造和试验;2009年10月,沈鼓集团完成了《10万Nm3/h空分1/2增压机样机研制》科研立项,再次自筹资金1300万元,于2012年完成了制造和试验工作,完成了包括模型级开发、关键部件的加工方法、通流部分的表面处理等20多项专项试验验证。
在总设计师汪创华的激情鼓舞下,60多位技术人员热血沸腾地投入到10万Nm3/h空分压缩机的设计当中。对于技术设计人员来说,10万Nm3/h等级空分压缩机组的设计由于采用全新结构,无论是压缩机、增压机的结构设计,还是密封、壳体的完成,都没有经验可借鉴。面对巨大压力和困难,他们迎难而上,依靠成熟先进的大型、超大型离心压缩机技术和大型轴流压缩机技术,在掌握轴流加离心优化匹配技术和多级多轴多转速齿轮组装技术的基础上,进行了技术和机组性能的再优化、再创新、再升级。
沈鼓集团科协在项目创新过程中也发挥了重要作用,针对直齿端齿盘技术问题,沈鼓集团科协多方调研,积极联系国内相关专业的专家、教授,最终通过沈阳市科协的帮助,成功与中南大学钟掘院士达成合作。在钟掘院士的指导下,中南大学为沈鼓集团培养了多名直齿端齿盘技术人员(掌握直齿端齿盘的CAD/CAM方法及软件),突破了直齿端齿加工的技术难题,首次实现了直齿端齿的国产化加工制造,为10万空分项目的国产化提供了技术支撑。 重大意义和深远影响 2018年4月26日,中国机械工业联合会与中国通用机械工业协会在北京组织召开了“10万Nm3/h等级空分装置用空气压缩机组”产品鉴定会,经质询和讨论,与会专家形成鉴定意见:10万等级空分装置用空气压缩机组填补了国内空白,是装备国产化的重大技术突破,机组技术性能达到了国际同类产品先进水平,其中机组操作性和工况适应能力等居国际领先水平。
国家能源局总经济师李冶对10万Nm3/h制氧量空分装置压缩机组实现国产化的重大意义总结道:一是国家重大技术装备的技术创新成果;二是我国高端装备制造业的标志性产品;三是将成为推进我国重大技术装备实现“走出去”战略的重要手段;四是体现了东北老工业基地的战略地位和以沈鼓集团为代表的大型国有企业的支柱性地位。
|