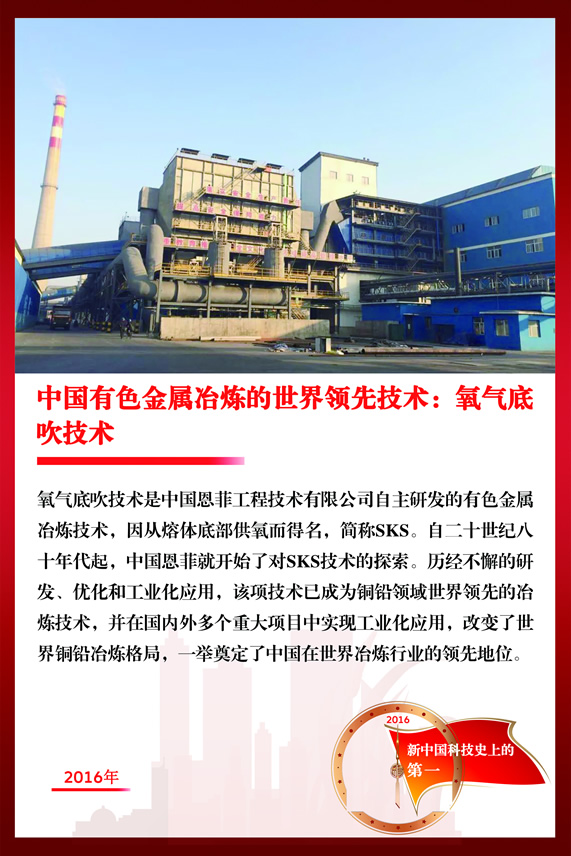
成果简介 氧气底吹技术是中国恩菲工程技术有限公司(以下简称“中国恩菲”)自主研发的有色金属冶炼技术,因从熔体底部供氧而得名,简称SKS。自二十世纪八十年代起,中国恩菲就开始了对SKS技术的探索。历经不懈的研发、优化和工业化应用,该项技术已成为铜铅领域世界领先的冶炼技术,并在国内外多个重大项目中实现工业化应用,改变了世界铜铅冶炼格局,一举奠定了中国在世界冶炼行业的领先地位。 历史背景 长期以来,国内现代强化冶炼技术几乎全部都依靠国外引进,对外技术依赖严重,长期受制于人。二十世纪八十年代后,伴随发达国家对环保要求的日趋严格,为淘汰传统的烧结—鼓风炉传统炼铅工艺,各国纷纷开展了新的炼铅工艺的研究工作,包括QSL一步炼铅工艺、Kivcet工艺、Kaldo炼铅工艺、顶吹炼铅工艺等。
虽然国外开发的冶炼技术多种多样,但直接引进到国内会带来一些工程问题,且成本相对较高。为扭转技术受制于人的被动局面,同时为解决困扰我国冶炼过程中存在的污染问题,提高自主创新能力和技术的适用性,实现低碳环保的绿色冶炼,中国恩菲高级顾问专家、全国勘察设计大师蒋继穆带领着中国恩菲的冶炼专家,聚焦低碳、环保、高效的有色冶金新工艺,开启了氧气底吹熔炼技术的研发之路。 创新历程 中国恩菲研发氧气底吹熔炼技术的征程始于铅冶炼。1983年9月,经国家科委批准,氧气底吹炼铅课题被列入国家“六五”计划,北京有色冶金设计研究总院(中国恩菲前身)、水口山矿务局(湖南水口山有色金属集团有限公司前身)牵头进行了大量小型试验。1985年12月,中国恩菲设计的年产3000吨粗铅的半工业试验成套装置建成,至1987年11月底共进行了10批次试验,完成熔炼895吨铅精矿,产出粗铅342吨。为解决产出的高铅渣没法处理和金、银分散的问题,1990年7月,中国恩菲牵头组织专家团队,在原有底吹炉内进行了铜精矿与含金黄矿1∶1的混矿熔炼试验,并获得圆满成功。1997年9月,为满足国家日趋严格的环保要求,实现“烧结锅—鼓风炉炼铅工艺必须于2000年前全部淘汰”的目标,中国恩菲继续开展研究,利用原有底吹熔炼炉和1.5平方米小型鼓风炉开展底吹熔炼—鼓风炉还原炼铅工艺试验。试验通过适度提高鼓风炉料焦率、降低鼓风熔炼强度,成功将渣含铅量降低到3%以下,达到与熔炼烧结矿同样的水准。
为进一步提升节能环保效果,中国恩菲技术团队不断寻求新的突破,向着更低能耗的方向迈进,研发出氧气底吹熔炼—熔融侧吹还原法、氧气底吹熔炼—熔融底吹电热还原法炼铅技术。最终,第三代氧气底吹熔炼技术实现耗煤量接近理论值。
在持续优化氧气底吹炼铅技术的过程中,中国恩菲依托“造锍捕金”试验,逐渐将该技术延伸到铜冶炼领域,开启了底吹炼铜和造锍捕金技术的产业化开发应用道路。在铜冶炼领域,中国恩菲对SKS技术进行优化改造,将工艺气体直接鼓入铜锍层,鼓入的冲击力以及气泡的上升和膨胀,给熔体带来很大的搅动能量。这种技术具有烟气带走热量少、炉体热损失小、渣量少、操作温度低等多种优势,熔炼过程完全自热,无需添加任何燃料,是国际领先的低碳冶炼工艺。 重大意义和深远影响 作为中国恩菲在有色冶炼领域重要的科技创新成果,SKS因其节能、环保、原料适应性强等突出优势,被海内外超过70家冶炼企业采用,两次荣获国家科技进步奖。目前,SKS已成为基本金属产业转型发展的关键支撑技术、提升国家有色金属产业国际竞争力的核心保障技术、国际产能与装备制造合作的引领技术、国际基本金属冶炼优先技术,成为中国有色行业在国际上一张自主创新的名片。国际知名行业媒体——英国《金属导报》曾这样评价SKS:“氧气底吹冶炼技术指明了金属冶炼行业乃至多个领域未来十年、数十年,乃至上百年的发展方向。”
|